OWNER:
Henry Boot Development
ENGINEER:
BWB
GENERAL CONTRACTOR:
Bowmer & Kirkland Limited
MAIN FIGURES:
1,293 Dynamic Replacement Pillars
38,620 m2 Dynamic Compaction
8,589 Controlled Modulus Columns
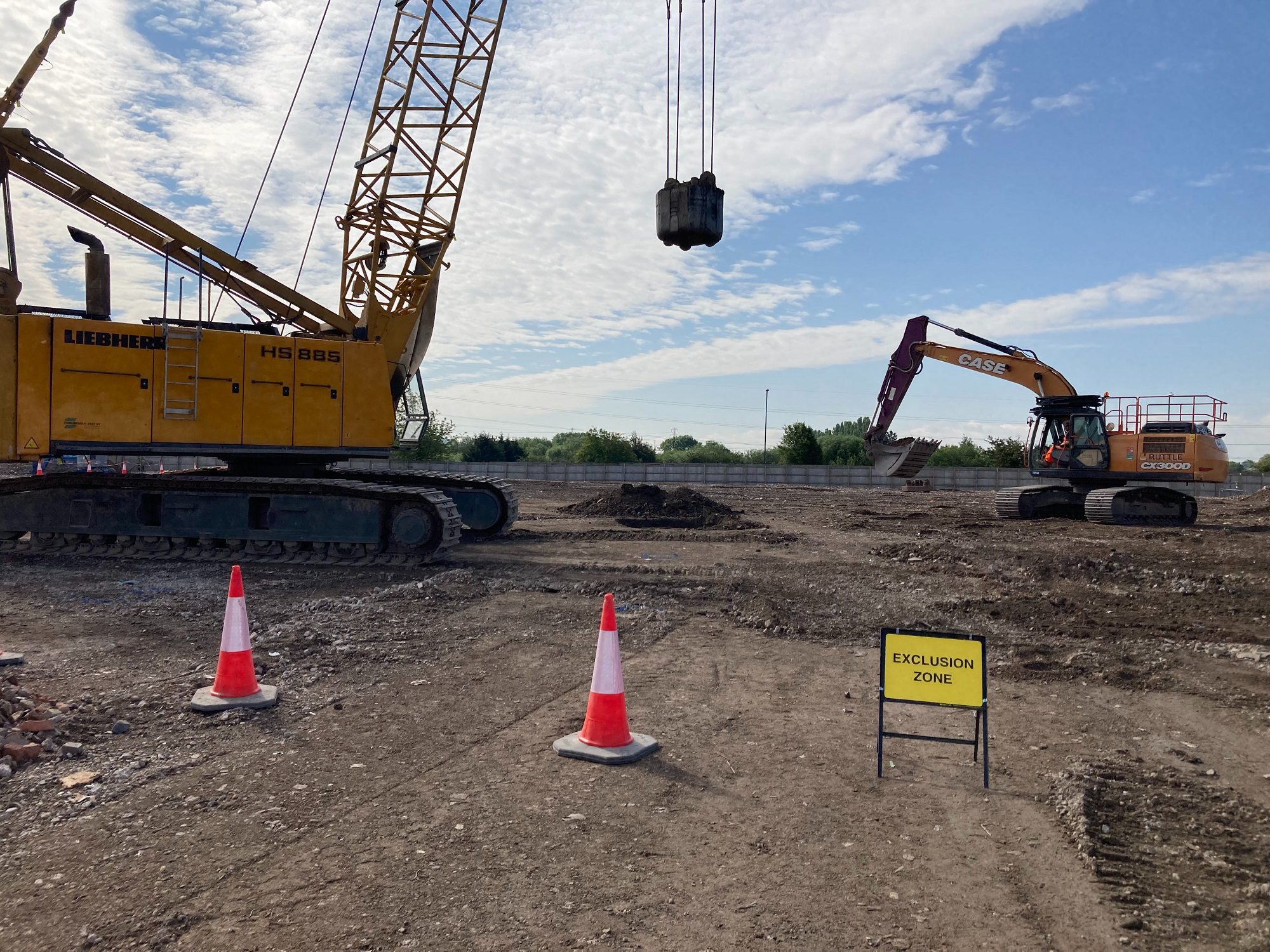
Project Details
The project consisted of the construction of 5 new commercial units and associated service yards and access roads on the former Imperial Tobacco industrial site.
Ground Conditions
The soil conditions consisted of granular made ground between 1 to 2m thick, above landfill material 3 to 4m thick, overlying 2 to 3m thick soft cohesive alluvium acting as a liner below the landfill material. Below the alluvium, dense sands and gravels above sandstone were encountered.
Solution
Regarding the challenging soil conditions (landfill material and soft alluvium), Menard UK has been approached at early stage to devise a ground improvement solution to allow the project to be within budget. Menard UK offered a combination of Dynamic Replacement (DR) below the externals and Dynamic Compaction (DC) + Controlled Modulus Columns (CMC) below the buildings to allow the construction of pad foundations designed at 200kPa SLS and ground bearing slabs loaded at 50kPa UDL. The DR were stopped within the alluvium without punching through to ensure no contamination from the landfill material would penetrate the underlying aquifer (sands and gravels). The CMC system, due to the use of a displacement auger displacing the soil laterally and concerting during the extraction of the tool was accepted by the EA as a viable solution.
Sustainable Development
In addition to the usual embodied carbon footprint that ground improvement solutions have against traditional piling solutions, Menard UK went a step further by using recycled aggregate to form the Dynamic Replacement pillars, limiting therefore the carbon footprint of the overall project.