OWNER:
Henry Boot Development (HBD)
ENGINEER:
BWB Consulting
GENERAL CONTRACTOR:
Readie Construction
MAIN FIGURES:
7,598 Controlled Modulus Columns
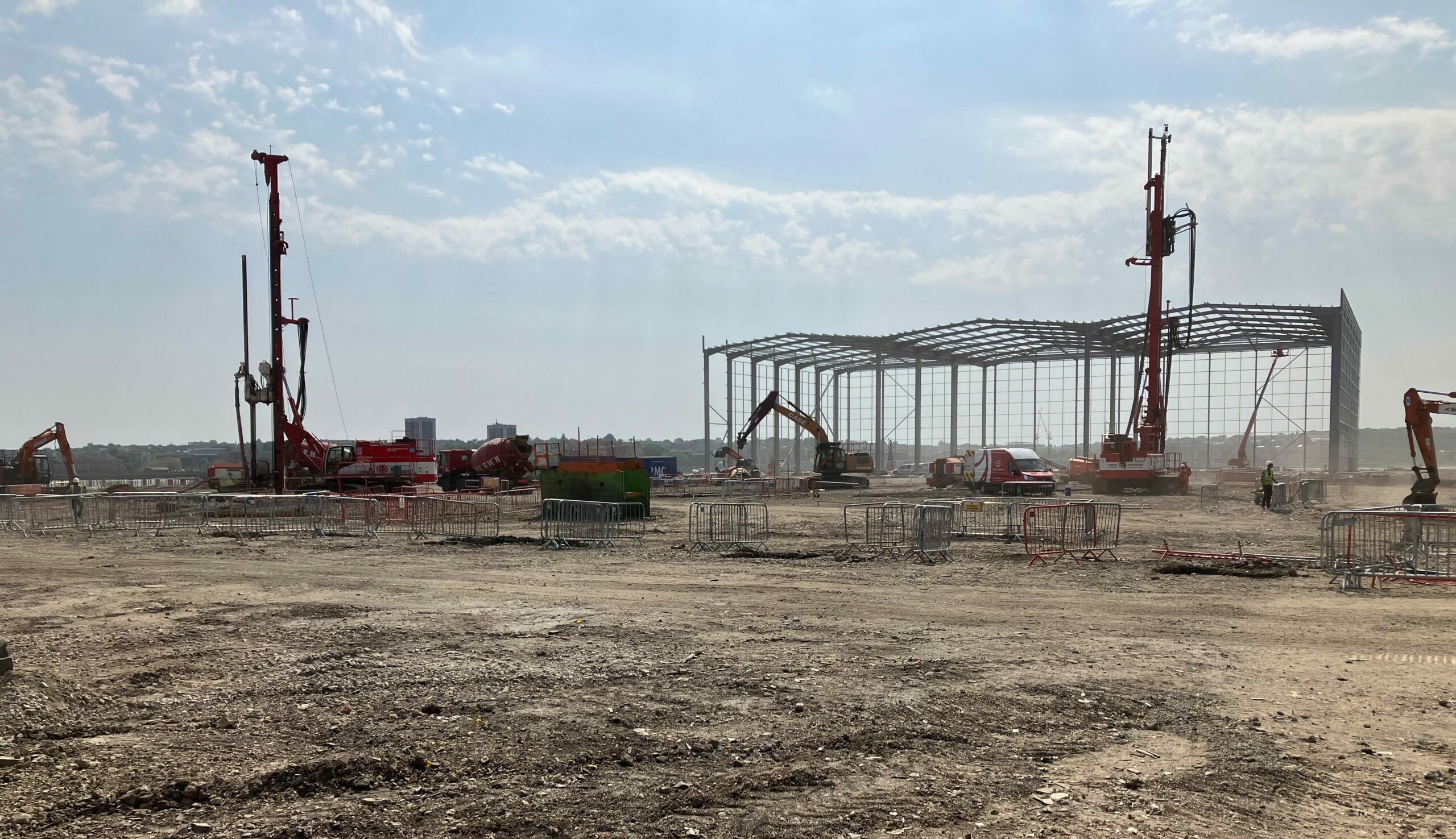
Project Details
Readie Construction Limited approached Menard UK to carry out ground improvement in the form of CMC’s under 3 new commercial units and adjoining ancillary structures. The project, which ran over the course of a 5 month period proposed difficult logistical challenges to the site team working not only in close proximity to ground workers and steel erectors but also another trade completing works using large cranes.
With the concrete batching plant being located around the corner from the site location, the operational team were able to achieve record breaking production enabling the contract to perform well and be completed with a high level of quality much to the delight of the project stakeholders.
Ground Conditions
Upon receipt of the CPT’s, the ground conditions across all 3 of the units were fairly homogeneous. The typical ground conditions present on site were made ground underlain by very soft to firm clays (alluvium) down to maximum 17 m above river terrace deposits and chalk. From the calibration drillings, it was clear that once through the made ground the drilling conditions were favourable for this type of drilling enabling the site team to speed up the production process.
Solution
Menard UK offered a bespoke solution of Controlled Modulus Columns (CMC) rigid inclusions allowing the construction of conventional shallow foundations. This ground improvement solution brought significant benefits to the overall project compared to a traditional piling scheme, by reducing the embodied carbon footprint, accelerating and simplifying the construction sequence, and reducing costs. The CMC has been designed to reduce the residual settlements to 25 mm, with relative differential settlements lower than 1/500, and enhance the allowable bearing capacity to 200 kPa beneath the footings.
The final figures upon project completion were around 7,600 CMC’s installed with a total linear meterage drilled of more than 121,000 linear metres. The CMC works were completed on site and have been verified through a thorough quality control system. In such a constrained environment, coordination with other trades was paramount and site-specific measures have been implemented to ensure that the works were conducted safely.
Sustainable Development
The use of Controlled Modulus Columns (CMC) instead of deep CFA piles greatly reduced the embodied carbon of the construction, by removing the need for heavy carbon-emitting structures such as pile caps and suspended slabs. Thanks to the additional site investigation (CPT), the design of the CMC has also been optimised, leading to a further reduction in the embodied carbon. Finally, the use of a a low-carbon concrete with a high proportion of GGBS instead of cement also contributed to reduce the CO2 emissions.