OWNER:
Lee Valley Regional Park Authority
ENGINEER:
Ramboll
GENERAL CONTRACTOR:
Buckingham Group
MAIN FIGURES:
1,234 Controlled Modulus Columns (CMC) installed
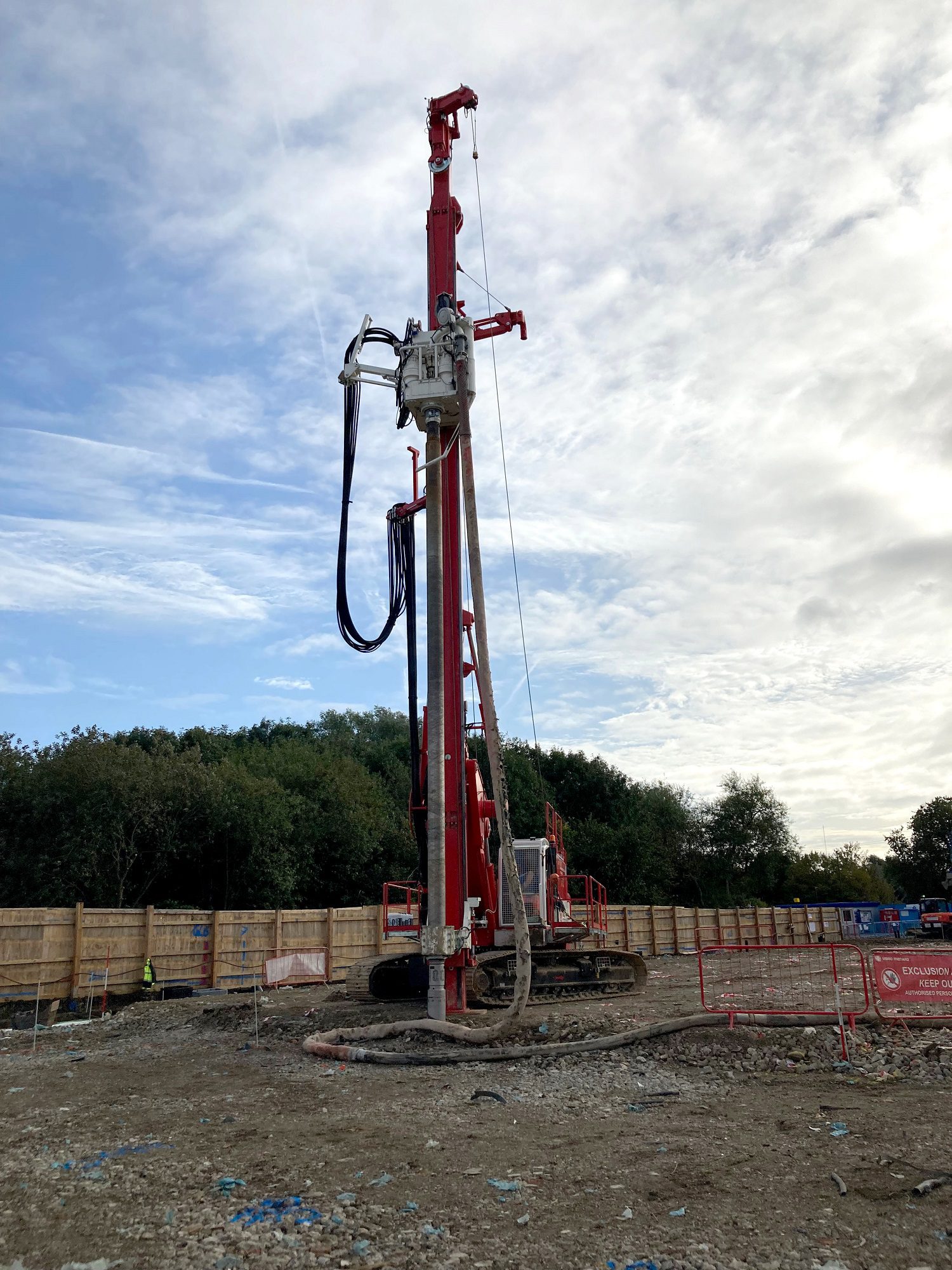
Project Details
Following successful collaboration on previous similar schemes, Buckingham Group approached Menard to find an alternative efficient foundation solution for the redevelopment of the Lee Valley Ice Centre in Leyton, London, where the base design called for a piled solution with suspended slab. This new centre, with a footprint of more than 7,000 m², will include two new Olympic-sized ice rinks and will replace the three decade old building, doubling the capacity (800 spectators) and offering an array of leisure facilities such as gym, café and community spaces.
Ground Conditions
The initial site investigation confirmed the stratigraphy being typical of this area of London, with a top layer of Made Ground, over very soft clay (Alluvium) underlain by dense sands (River Terrace Deposits) above stiff clay (Lambeth Group), Thanet sands and chalk. To fine-tune the CMC design, further ground investigation by Cone Penetration Tests (CPT) has been carried out. These CPT confirmed the overall ground conditions and showed that the Alluvium layer was too soft for Vibro Stone Columns (risk of bulging failure) and that the River Terrace Deposits were encountered at a depth of about 4 to 6 m from the existing ground levels.
Solution
Menard designed and installed a solution of Controlled Modulus Columns (CMC) rigid inclusions, to avoid piling and allow the use of conventional shallow foundations (pad footings and ground bearing slabs) to support the building. This ground improvement solution brought significant benefits to the overall project, by reducing the embodied carbon footprint, accelerating and simplifying the construction sequence, and reducing costs. An SLS allowable bearing capacity of 250 kPa was achieved beneath the footings with CMC.
The design included a specific analysis to prove that the CMC had no impact on a nearby National Grid tunnel and close coordination with the Engineer was required to cater for the various changes. The piles from the previously existing ice centre were also kept in the ground, so the CMC positions had to be carefully adjusted accordingly.
The works have been completed in less than 3 weeks on site, ahead of programme, with a strict quality control comprising plate load tests on isolated CMC, compressive strength tests on concrete samples and drilling/concreting logs from the rig computer.
Sustainable Development
The use of Controlled Modulus Columns (CMC) instead of 15 m deep CFA piles greatly reduced the embodied carbon of the construction, by reducing the quantities of heavy carbon-emitting materials such as concrete (no concrete piles, thinner ground bearing slab) and steel (no pile caps, conventional pad/strip footings). Furthermore, the concrete mix design used a proportion of GGBS instead of cement (low-carbon concrete), leading to a further reduction of the overall carbon footprint of the project.