OWNER:
IM Properties
ENGINEER:
Fairhurst
GENERAL CONTRACTOR:
Winvic Construction
MAIN FIGURES:
2,114 Dynamic Replacement pillars
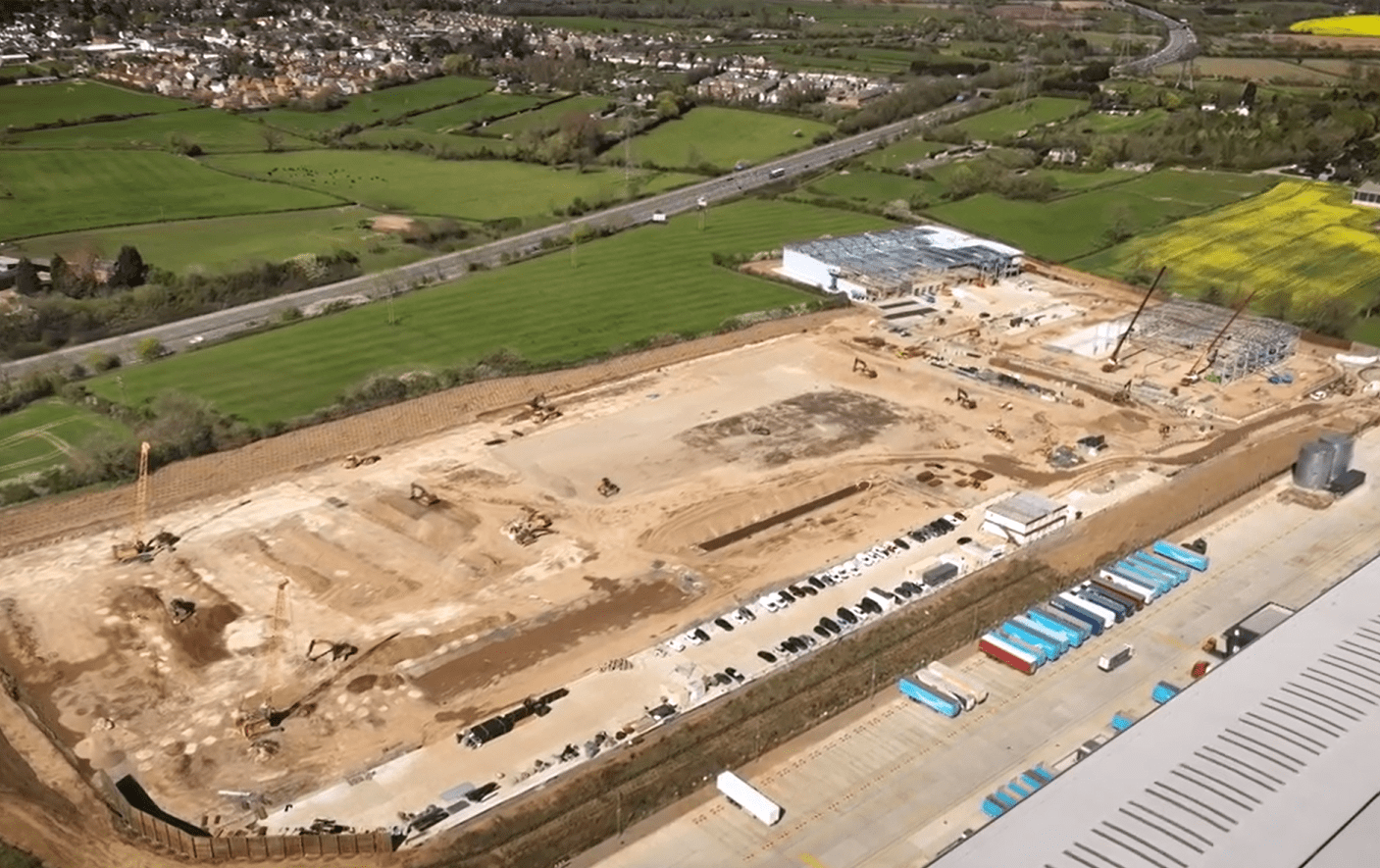
Project Details
Following the successful completion of ground improvement works on the previous phase of this Hinckley Park (Leiceistershire) logistics development in 2019, Winvic approached Menard to find a cost-effective foundation solution for the new phase of the works, comprising 3 warehouse units covering more than 40,000 m² in total. This prospective development had to be designed to a FM2 specification to support a uniformly distributed load of 50 kPa, whilst the frame brought point loads of up to more than 3,000 kN SLS. The settlement criteria were specified to 25 mm of residual settlements, with relative differential settlements limited to 1/600.
Ground Conditions
The initial site investigation revealed the presence of very soft to soft clay of the Oadby Member down to about 2 to 5 m (with CPT cone resistance as low as 0.5 MPa in some instances), above firm and stiff clay (Oadby Member) interbedded with some layers of dense sand and gravel (Wolston Sand and Gravel). The Mercia Mudstone bedrock was encountered at depth. The cut & fill works carried out prior to Menard’s intervention on this sloped site included the installation of up to 3 m of fill consisting of in-situ lime-treated material placed in layers. The characteristics of this upfill have been checked by additional site investigation using Cone Penetration Tests (CPT).
Solution
The earthworks being carried out on site prior to any ground improvement, the proposed solution had to consider the consolidation of the in-situ ground under the weight of the fill to happen during the construction period. The presence of very soft clay layers also prohibited the use of Vibro Stone Columns (VSC) due to the risk of bulging failure. Menard therefore offered a ground improvement solution of Dynamic Replacement (DR). This scheme enabled the construction of regular shallow foundations: pad footings with 200 kPa SLS allowable bearing pressure and conventional ground bearing slab, hence providing significant savings compared to a piling option. The DR pillars, arranged in a square grid of about 4.5 m spacing, were topped up with a 750 mm thick Load Distribution Mattress beneath the slab. Clusters of DR pillars (up to 3 pillars per pad) were also installed beneath the footings to support the structural steel frame. The detailed design of the ground improvement has been carried out with Finite Elements Models and analytical calculations. The 2,000+ DR pillars were installed in 3 months on site, with 2 DR cranes. The compaction of the DR pillars has been verified by means of CPT.
Sustainable Development
Dynamic Replacement is a very low-carbon solution because only stones (and no concrete) are used for the ground improvement and it allows the construction of conventional shallow foundations. Menard also sourced recycled aggregates to form the DR pillars, reducing the overall embodied carbon footprint of the solution.
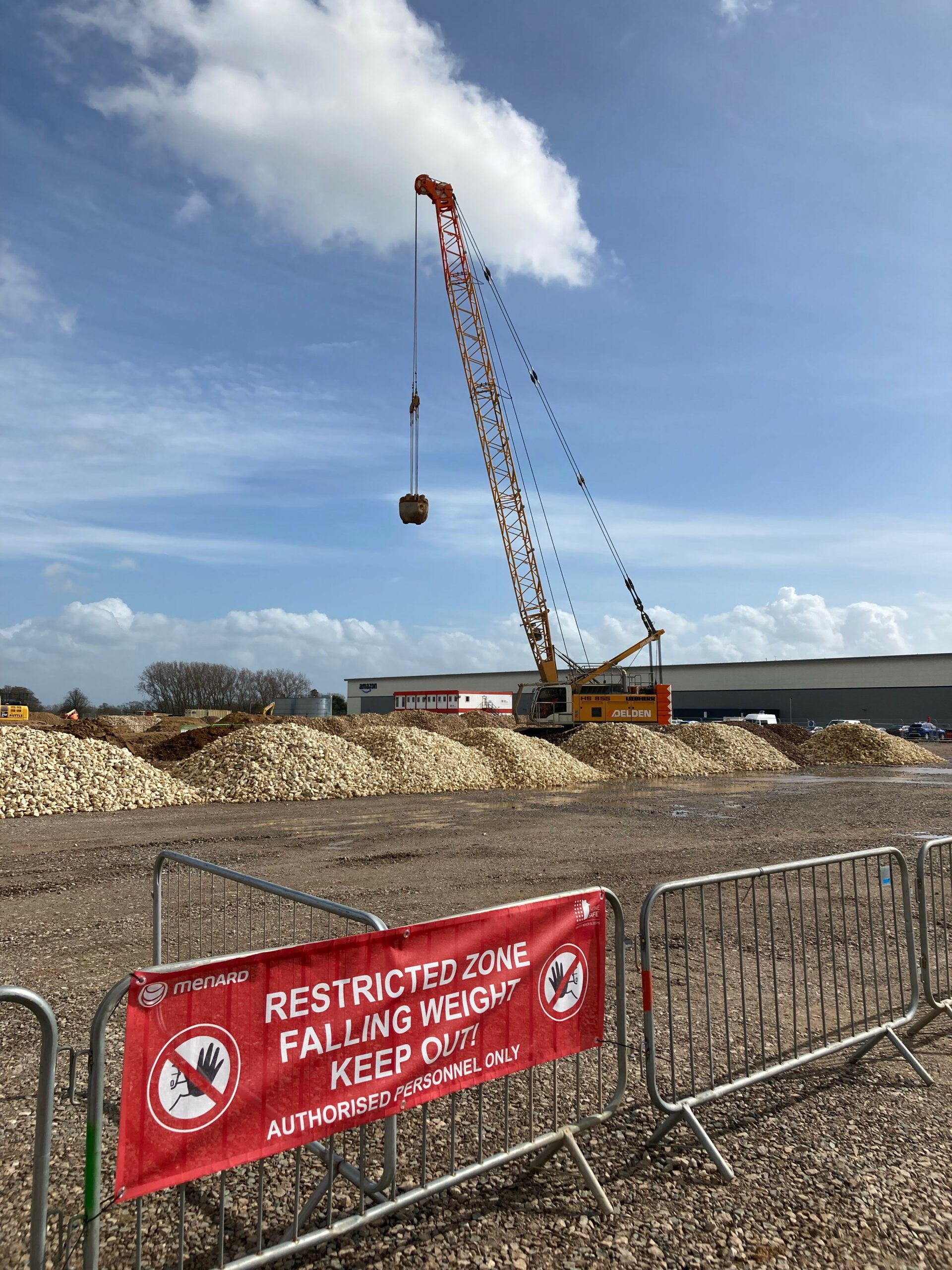