OWNER:
Bloom Developments
ENGINEER:
Burrows Graham
GENERAL CONTRACTOR:
MCS Group
MAIN FIGURES:
503 Controlled Modulus Columns
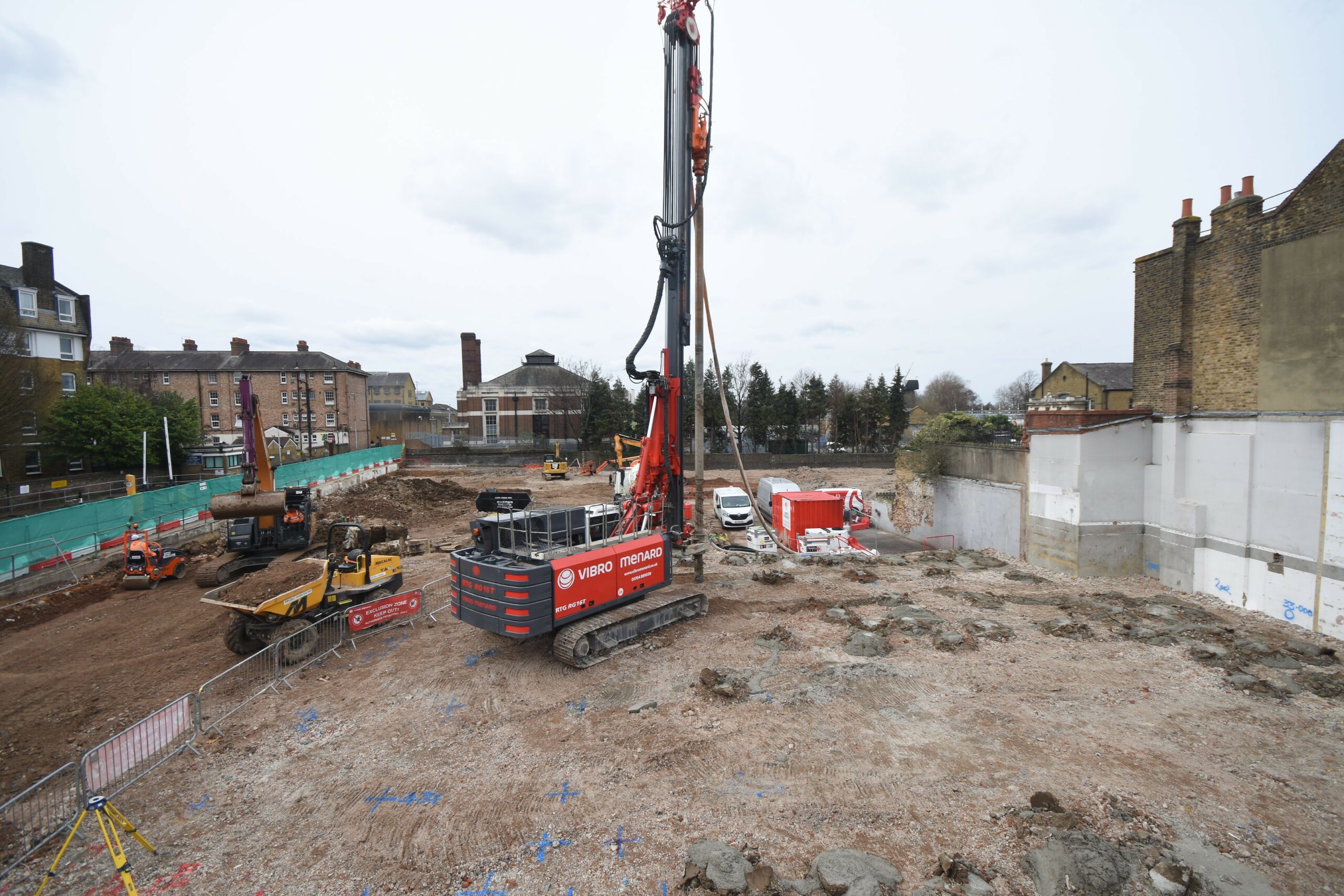
Project Details
MCS approached Menard UK to find a cost-effective alternative foundation solution for a development by Bloom of two industrial ultra-urban units totalling around 1,600 m² of ground floor in a prime location in Brixton, London. The two-storey office and warehouse buildings are designed to a FM2 specification to support a uniformly distributed load of 37.5 kPa, whilst the frame structure brought point loads of up to 3,000 kN SLS. The site is located in a very constrained urban environment, with one block in close proximity to a water main (Thames Water) to the North and the other block being built just adjacent to an existing and live supermarket.
Ground Conditions
The initial site investigation revealed relatively homogeneous ground conditions, with a few meters of heterogeneous made ground underlain by soft becoming very stiff clay (London Clay formation). At the request of Menard UK, additional CPT have been carried out across the whole site to map more precisely the variations of the ground conditions and inform the detailed CMC design.
Solution
Menard UK offered a bespoke solution of Controlled Modulus Columns (CMC) rigid inclusions allowing the construction of conventional shallow foundations. This ground improvement solution brought significant benefits to the overall project compared to a traditional piling scheme, by reducing the embodied carbon footprint, accelerating and simplifying the construction sequence, and reducing costs.
The CMC installation process is also vibration-free, which was key on this scheme due to the presence of adjacent structures (supermarket building and water main). The CMC have been designed to reduce the residual settlements to 25 mm, with relative differential settlements lower than 1/500, and enhance the allowable bearing capacity to 200 kPa beneath the footings.
The final detailed design comprised more than 500 CMC taken to depths about 6 to 7 m. The CMC works have been completed safely, on time (in less than 3 weeks) and have been verified through a thorough quality control system.
Sustainable Development
The use of Controlled Modulus Columns (CMC) instead of deep CFA piles greatly reduced the embodied carbon of the construction, by removing the need for heavy carbon-emitting structures such as pile caps and suspended slabs.
Furthermore, the use of a low-strength and low-carbon concrete, with a mix design using a high proportion of GGBS, led to a further reduction of the overall carbon footprint of the project.